Fasteners and Machining: Enhancing Longevity and Efficiency in Production
Fasteners and Machining: Enhancing Longevity and Efficiency in Production
Blog Article
Unveiling the Ins And Outs of Fasteners and Machining Procedures for Ideal Performance
In the world of engineering and production, the choice of fasteners and the ins and outs of machining processes play a crucial function in identifying the best performance and resilience of an item. From the seemingly simple job of selecting the right sort of fastener to the complicated accuracy machining methods used, every step in this procedure demands thorough interest to detail. As we begin on this expedition right into the world of bolts and machining, we will discover the refined yet vital aspects that can significantly affect the efficiency and high quality of the end product, clarifying the usually neglected facets that can make all the distinction in accomplishing ideal performance.
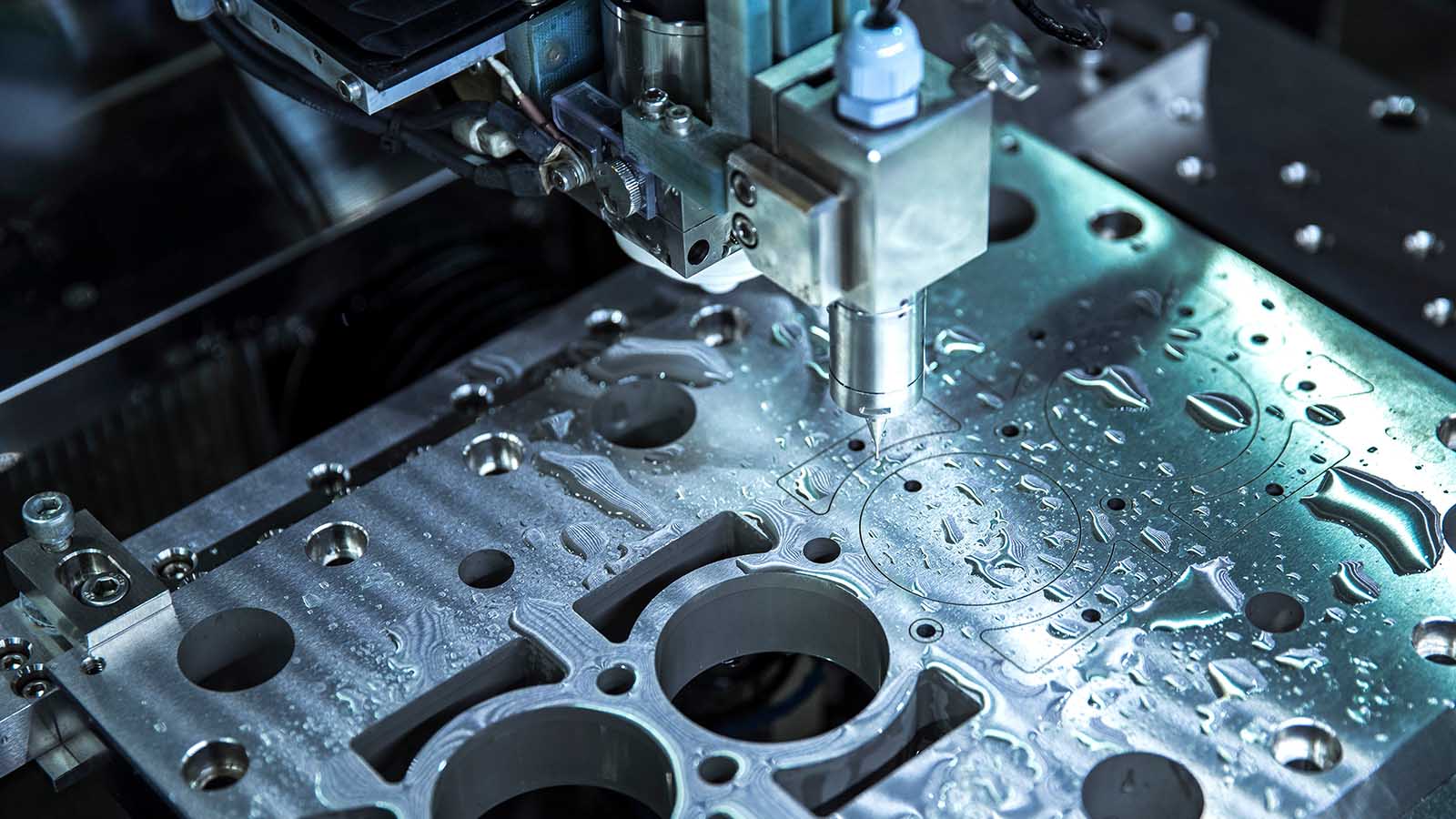
Value of Appropriate Fastener Choice
Choosing the appropriate bolts is critical in making sure the structural integrity and long life of any type of mechanical assembly. Bolts play an essential role in holding parts with each other securely, with the appropriate selection contributing significantly to the total performance and integrity of the setting up. When choosing bolts, elements such as product compatibility, environmental conditions, load-bearing ability, and ease of installment need to be thoroughly considered to ensure optimal efficiency.
Improper bolt selection can cause a range of problems, consisting of loosening, deterioration, and also structural failing. Using bolts that are not suited to the certain needs of the assembly can endanger its functionality and present security threats. For that reason, designers and designers must thoroughly review the application needs and choose bolts that meet or exceed the essential standards and specs.
Additionally, the right bolt option process involves evaluating the joint style, prepared for tons, vibration degrees, and prospective thermal development or tightening to ensure that the selected fasteners can endure the operating problems successfully. By focusing on proper fastener selection, manufacturers can boost the quality, sturdiness, and performance of their mechanical assemblies.
Types and Qualities of Fasteners
An important aspect of mechanical settings up lies in understanding the varied types and unique features of bolts made use of in different industrial applications. Bolts are vital components that hold frameworks together, ensuring security and functionality.
Screws are threaded fasteners that are frequently used to join 2 or more elements together. Screws are similar to screws yet are usually used with a nut to produce a secure joint. Nuts are inside threaded fasteners that mate with screws to hold components with each other. Washers are slim plates that distribute the tons of a bolt, avoiding damages to the material being attached. Rivets are permanent bolts that are hammered or pressed into area. Pins are used for placement or to secure elements momentarily.
Comprehending the features of each type of fastener is important for selecting the right one for a certain application, making certain optimum efficiency and dependability of the mechanical assembly. Fasteners and Machining.
Precision Machining Strategies for Effectiveness
The complex style requirements of numerous fasteners necessitate using accuracy machining methods for optimal efficiency in making procedures. Precision machining is crucial in making certain that bolts meet the specific specs needed for their desired application. Among the primary strategies used in accuracy machining is Computer system Numerical Control (CNC) machining, which enables high degrees of accuracy and repeatability in the production of bolts. CNC equipments can executing complicated cuts and forming operations with marginal human intervention, leading to boosted efficiency and uniformity in the manufacturing procedure.
In enhancement to CNC machining, other accuracy techniques such as grinding, milling, and turning are generally used to accomplish the limited tolerances needed for fasteners. These strategies allow manufacturers to produce bolts with smooth surfaces, accurate measurements, and high architectural stability. By making use of precision machining methods, manufacturers can improve the high quality of bolts, lower material waste, and improve general manufacturing performance. The use of advanced machining processes helps guarantee that bolts satisfy market standards and customer expectations for performance and dependability.

Variables Influencing Machining Refine Efficiency
Numerous variables play a substantial duty in establishing the efficiency of machining procedures in the production of bolts. Optimizing these parameters based on the specific requirements of the bolt being generated is vital to attaining specific and cost-efficient machining.
Maker rigidity and important link security also play a crucial duty in identifying machining procedure performance. An educated operator can make real-time changes, troubleshoot problems successfully, and make sure that the machining process runs smoothly, inevitably impacting the last high quality of the bolt.
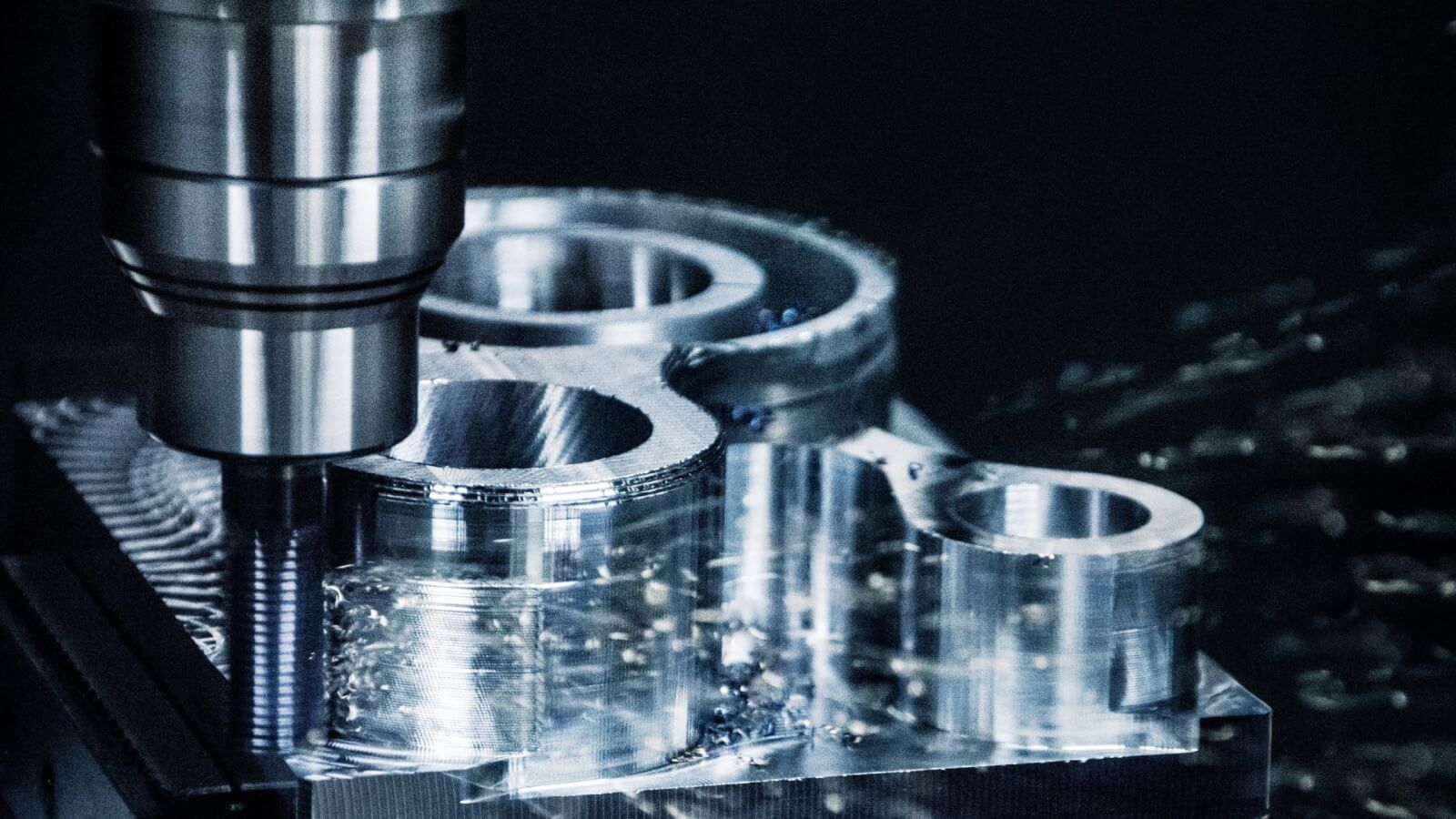
Quality Assurance Steps in Manufacturing
Factors influencing machining procedure efficiency, such as reducing tool selection and device security, straight effect the implementation of quality control measures in production. Quality assurance steps are crucial in making certain that items satisfy the required specifications and criteria. In the manufacturing procedure, different techniques are employed to keep high quality standards. Evaluation and testing play a crucial duty in determining any inconsistencies from the preferred outcome. Normal maintenance of machining equipment is additionally important to copyright top quality control. Calibration of machines and devices is required to ensure exact and accurate production processes. In addition, executing standard operating procedures and methods can assist in keeping consistency and high quality throughout the assembly line. Quality assurance determines not just concentrate on completion product yet also this post on every phase of the manufacturing process to stop defects and errors. By adhering to rigorous quality assurance procedures, suppliers can enhance consumer contentment, construct a credibility for integrity, and eventually accomplish optimum efficiency in their machining procedures.
Final Thought
In final thought, picking the appropriate bolts and making use of accuracy machining techniques are important for optimal performance in manufacturing processes. Recognizing the kinds and features of bolts, in addition to aspects affecting machining process performance, can lead to improved efficiency and quality assurance measures. By paying attention to these intricacies, suppliers can attain greater levels of efficiency and dependability in their products.
In the realm of design and production, the selection of fasteners and the details of machining procedures play a critical role in establishing the utmost performance and sturdiness of a product (Fasteners and Machining). One of the key methods used in accuracy machining is Computer system Numerical Control (CNC) machining, which enables high degrees of accuracy and repeatability in the manufacturing of bolts. The use of sophisticated machining processes helps make certain that fasteners fulfill get more market standards and client expectations for efficiency and reliability
In verdict, choosing the appropriate fasteners and making use of precision machining strategies are necessary for optimal efficiency in manufacturing procedures. Understanding the kinds and characteristics of bolts, along with factors influencing machining procedure performance, can lead to boosted efficiency and high quality control measures.
Report this page